Concrete Testing Techniques: Our Comprehensive Guide
Understanding the properties and condition of concrete is crucial for a successful flooring project. This page will explore various concrete testing techniques that help us ensure the quality, safety, and longevity of your flooring.
Why Concrete Testing Matters
Concrete testing is the cornerstone of any flooring project, especially when applying coatings like epoxy. Discover why testing is critical, the problems it helps prevent, and the long-term benefits it brings to your flooring project.
Types of Concrete Tests
Moisture Test:
This test determines whether there's an excess amount of moisture in the concrete. Two common methods include the Calcium Chloride Test and the Relative Humidity Test. The Calcium Chloride Test measures the rate of moisture vapor emission from the concrete surface. In contrast, the Relative Humidity Test uses in-situ probes to measure the moisture levels within the slab.
Concrete Hardness Test:
Also known as the Schmidt Hammer Test or Rebound Hammer Test, this method assesses the surface hardness of the concrete. The test involves a spring-loaded mass within a hammer that, when released, hits the concrete surface and then rebounds. The rebound distance is measured on a scale and can be used to estimate the concrete's compressive strength.
PH Test:
The PH level of concrete is essential as it impacts the adhesion of epoxy coatings. Concrete floors typically have a PH of 9 to 11, while epoxy works best in slightly acidic to neutral PH conditions. This test typically involves using PH paper or a digital PH meter.
Bond Test:
Also known as the Pull-off Test, it measures the adhesion strength between the concrete surface and the epoxy coating. A dolly (a flat disc) is glued to the concrete surface, and a pull-off adhesion tester is used to apply force until the dolly is pulled off. The force required to pull the dolly off gives an indication of the bond strength.
Abrasion Resistance Test:
This test measures the concrete's resistance to wear and tear. It involves abrading the surface and measuring the wear depth. The most common method is the Böhme abrasion test, where an abrasive material is ground onto the concrete surface using a disc.
Concrete Soundness Test:
This test is done by dragging a chain over the concrete surface or by using a hammer to tap the surface. The purpose is to detect any hollow sounds, which could indicate delamination or air gaps within the slab.
Each of these tests provides crucial information about the condition of the concrete and helps professionals like us determine the right preparation method for the concrete and the type of epoxy for the project.
Test Interpretation
Interpreting the results of concrete tests requires a deep understanding of concrete properties and the requirements of the epoxy flooring systems. These test results provide a wealth of information that informs every step of the flooring installation process.
How to Interpret Like One of Our Pros
Moisture Tests:
The results from moisture tests like the Calcium Chloride Test and the Relative Humidity Test are expressed as a rate of moisture vapor emission (for example, pounds of moisture over 1,000 square feet in 24 hours). If the moisture content is too high, it can prevent proper adhesion of the epoxy to the concrete, leading to flooring failures like blistering or peeling. Depending on these results, professionals may choose to install a moisture barrier or select a specific epoxy coating designed to cope with higher moisture levels. For most epoxy coatings, a 'good' result is a value less than 3 lbs. A 'bad' result is a value greater than 3 lbs, suggesting that a moisture mitigation system might be required before epoxy application.
Concrete Hardness Tests:
The Rebound Hammer Test provides an estimate of the concrete's compressive strength. If the concrete is too soft, it may not be suitable for certain heavy-duty epoxy systems. Conversely, very hard concrete may require more aggressive preparation methods to ensure good adhesion. For most industrial and commercial floors, a 'good' result is a compressive strength greater than 3000 psi, while anything less can be considered as 'bad', and may require a surface hardener or densifier before applying the epoxy.
PH Tests:
The results of PH tests help determine whether the surface is too acidic or too alkaline for the epoxy coating. Most epoxy coatings require a slightly acidic to neutral PH for optimal adhesion. If the concrete is outside this range, surface treatments may be needed to correct the PH level. Concrete PH tests ideally should result in a value between 6 and 9. A 'good' result is a PH within this range, and anything less than 6 (too acidic) or greater than 9 (too alkaline) is considered 'bad'. These cases may require PH adjusting treatments before applying the epoxy. This can include Acid Etching which is used for alkaline pH and is often muriatic (hydrochloric or a buffered phosphoric acid solutions. Alkali Detergents are used for low pH (acidic) concrete to neutralize the surface. These detergents are typically applied and scrubbed into the surface and then thoroughly rinsed. Buffer Solutions resist changed in pH and brings the surface towards neutral levels. Epoxy Primers are as the name states, an epoxy primer that is designed to tolerate wider ranges of pH and can be used to seal off a slab that's either too acidic or alkaline which prevents undesired pH levels from affecting subsequent epoxy layers.
Bond Tests:
The results from the Pull-off Test can help identify any potential adhesion problems before the epoxy is applied. If the bond strength is low, it may indicate issues with the concrete's surface condition that need to be addressed, such as contamination or insufficient surface roughness. A 'good' result typically is a bond strength greater than 1.5 MPa. If the bond strength is less than 1.5 MPa, the result is 'bad', indicating that the surface may need additional preparation, such as grinding, shot blasting, or thorough cleaning.
Abrasion Resistance Tests:
The results from abrasion tests like the Böhme test give an indication of the concrete's resistance to wear. If the wear resistance is low, it may influence the choice of epoxy system, with high-build or aggregate-filled systems being chosen for their superior wear resistance. For the Böhme test, a wear index of less than 200 mm³ is considered a 'good' result, indicating high resistance to wear. A result of more than 200 mm³ suggests the concrete has low wear resistance, which may call for the use of a high-build or aggregate-filled epoxy system.
Concrete Soundness Tests:
If the soundness test results indicate hollow areas or delamination within the slab, these areas may need to be repaired before the epoxy coating is applied. Soundness tests like chain dragging or impact echo test help identify delaminated or hollow areas in the slab. A 'good' result means no detectable hollow sound, suggesting a sound slab. Any hollow sound is a 'bad' result, indicating that repairs may be needed before the epoxy application.
Understanding how to use these tests can help guide the selection of appropriate preparation methods and the most suitable epoxy system, ensuring the best possible quality, durable flooring solution.
Our recent case Study
To illustrate the importance of concrete testing and the effectiveness of corrective measures, let's consider a recent project our team undertook at a large manufacturing facility in Vaughan, Ontario.
Project Background & Flooring Challenge:
The client, a high-volume manufacturer of automotive parts, wanted to replace their worn-out floors with an epoxy coating system to improve the facility's aesthetics and durability. They had previously experienced coating failures due to unknown causes.
Our Diagnostic Approach:
Understanding the past coating failures, our team first performed a comprehensive battery of tests on the existing concrete floors. The tests revealed several issues, with the most significant being an excessively high concrete pH of 12.5, which was beyond the suitable range for epoxy coatings.
Strategic Solution & Execution:
To neutralize the high alkalinity, we recommended a treatment with a buffered phosphoric acid solution. We applied the solution, allowed it to react, then thoroughly rinsed and neutralized the surface to ensure no residual acid was left. Following the treatment, we performed a second pH test which indicated that the pH had dropped to a neutral 7.0, a level suitable for epoxy application.
With the pH corrected, we proceeded with the epoxy application. The client chose a high-build epoxy system known for its durability, chemical resistance, and ability to withstand heavy traffic. After preparing the surface through shot blasting, we applied a primer followed by multiple layers of the epoxy.
Successful Result & Long-Term Satisfaction:
The final result was a seamless, glossy epoxy floor that significantly improved the aesthetic appeal and functionality of the facility. Most importantly, the client hasn't reported any issues with the new coating since installation. This project demonstrated the vital role of concrete testing in ensuring the successful application of epoxy coatings and the effectiveness of pH adjustment treatments in rectifying concrete pH imbalances.
We remain committed to conducting thorough concrete testing on all our projects to identify and address potential issues before they can compromise the performance and durability of our epoxy flooring systems.
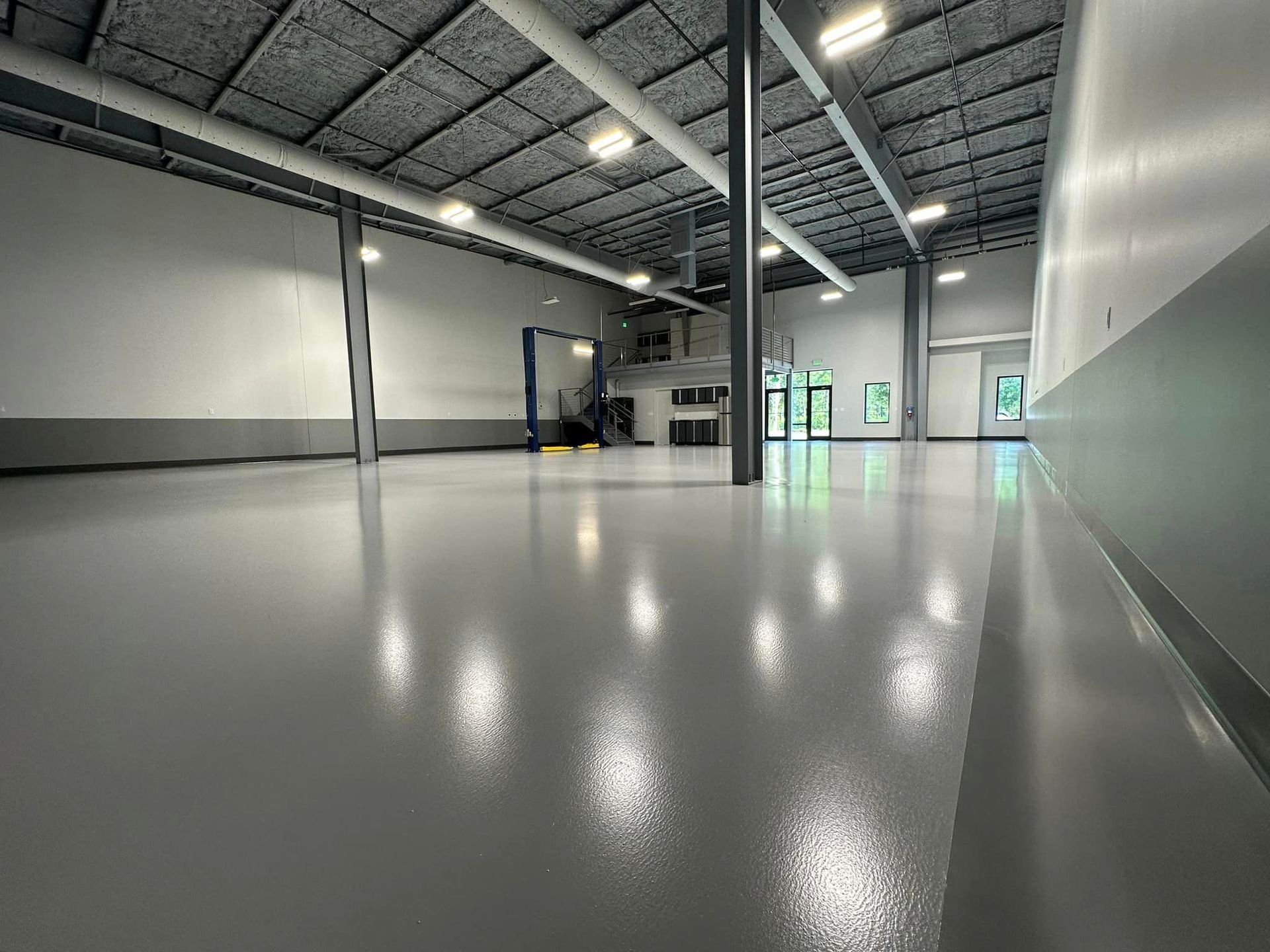
Our Testing Standards at Crystal Clear Epoxy
At Crystal Clear Epoxy, our commitment to quality is non-negotiable. Ensuring the best results for our clients begins with a deep understanding of the existing conditions of their concrete floors, and we accomplish this through rigorous testing protocols. The case of our automotive parts manufacturer client is a testament to our commitment. Their new high-build epoxy floor, catered to their high-traffic environment and made possible through careful testing and pH adjustment, stands as a shining example of the power of thorough concrete testing.
We perform a range of tests, each aimed at providing us with comprehensive data about the state of the concrete. From pH balance to moisture content, compressive strength to bondability, we leave no stone unturned. We know that every piece of information guides us to the best approach for the project, whether it requires pH adjustment treatments, surface preparation methods, or the selection of the right epoxy system.
Beyond the process, we invest in high-quality testing equipment, regular team training, and keeping abreast of the latest developments in concrete testing methodologies. This approach allows us to ensure that every project we undertake benefits from the most accurate data and informed decision-making.